TM 9-2320-302-34
0024 00-4
FLYWHEEL HOUSING REPLACEMENT - CONTINUED
0024 00
INSTALLATION - CONTINUED
CAUTION
To prevent damage to equipment, ensure contact between flywheel housing and end of bolt does not occur.
9.
Assemble dial indicator (8) to flex plate (9).
NOTE
Ensure dial indicator is positioned straight and square with flywheel housing bell face or inside bore of bell,
and has adequate travel in each direction.
10.
Check flywheel housing concentricity and bolting flange face runout.
11.
Ensure engine is in vertical position with flywheel housing (3) end up.
12.
Ensure end play is on one direction only. Tap end of crankshaft with soft hammer to position it toward one end of block.
NOTE
Maximum total indicator reading must not exceed 0.013 in (0.33 mm) for bore or face.
13.
Adjust dial indicator (8) to read zero. Rotate crankshaft one full revolution, taking readings at 90-degree intervals A,
B, C, and D (four readings each for bore bolting and face).
14.
If runout exceeds maximum limits, remove flywheel housing (3) and check for dirt or foreign material between flywheel
housing and cylinder block or oil pan mating surface. Clean mating surfaces, install flywheel housing (3) and perform
steps 9 through 13 to recheck runout.
15.
If readings are not within specification, replace flywheel housing (3).
16.
Repeat step 9 through 13 to check flywheel concentricity and bolting flange face runout for new flywheel housing.
17.
Install oil pan (WP 0028 00).
18.
Install starter (TM 9-2320-302-20).
19.
Install rear engine mounts (WP 0012 00).
END OF WORK PACKAGE
A
B
C
D
8
3
9
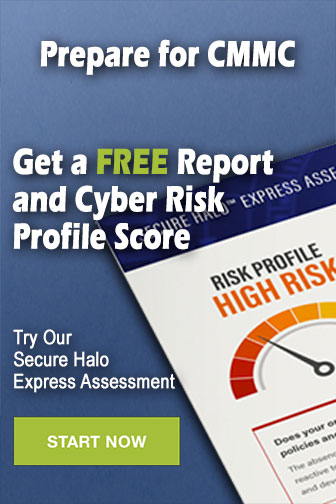