TM 9-2320-363-20-1
3. Bearings. Remove residue and oil stain from bearing races with crocus cloth.
NOTE
The following procedure is used with polished and machined steel parts not
protected by cadmium, tin, copper, or other plating or surface treatment. Bare
metal surfaces must be free of moisture when protective coating is applied.
4. Protective Parts. During repair operations, protect bare steel surfaces from rusting when not actually undergoing
repair work. Dip parts in, or spray them with, corrosion preventive compound. The same protective coating may be
applied to other metals to prevent rust. Aluminum parts may require protection in atmospheres having a high salt
content. Steel parts must always be protected.
CAUTION
Before welding, the following components must be disconnected: DDEC ECU,
ABS ECU, CTIS ECU, DATALOGGER, and batteries (TM 9-2320-363-20-2). If
welding on a trailer, it must be uncoupled from tractor/dump truck. Failure to
follow this caution may damage electronic components.
5. Welding. Welding and brazing may be used to repair cracks in external steel parts, such as brackets, panels, and
light framework. These repairs should be made only when replacement parts are not available. Do not weld or braze
castings, running parts, or parts under great stress, except in emergencies. When welding is required, refer to TM 9-
237.
6. Stud Installation. When installing studs in engine block and axle housings, use a driver designed for the stud to be
installed. A worn stud driver may damage the end thread. This makes it necessary to use a chasing die before a nut
can be screwed on. This procedure will remove cadmium plating and allow corrosion, which will make future
disassembly difficult and cause stud to be backed out with nut. Before driving a stud, inspect hole for chips and liquid.
Blow out any foreign matter. Start stud by hand. If it will not start into hole, it is too large or has defective end thread.
Before final insertion, coat thread with antiseize compound; turn stud in slowly to prevent overheating and galling of
casting metal.
7. Electrical Parts. Replace all broken, worn, or burned electrical wiring. Wires with several broken strands must be
replaced. Broken strands will increase the resistance of the wire and impair efficiency of electrical components,
especially the ignition system. When soldering is required, refer to TB SIG 222.
8. Hoses. Replace all broken, frayed, crimped, or soft flexible lines and hoses. Replace stripped or damaged fittings.
Replace entire flexible hose if fittings are damaged. Make sure hose clamps do not crimp hoses.
9. Fasteners. Replace any bolt, screw, nut, or fitting with damaged threads. Inspect tapped holes for thread damage. If
cross-threading or galling Is evident, retap the holes for the next oversize screw or stud. When retapping will weaken
the part, or when the cost of the part makes retapping impractical, replace the damaged part. Chasing threads with
the proper size tap or die may often be enough.
10. Dents. Straighten minor body dents by bumping with a soft-faced hammer while using a wooden block backing.
11. Sheet Metal Repair. Repair minor skin cracks by installing patches.
12. Mounting Holes. Reshape oval mounting holes to round. Drill to receive bushing with required Inner diameter. Stake
bushing in place with center punch.
GENERAL ASSEMBLY INSTRUCTIONS
1.
Preparation. Remove grease from new parts before Installation.
Change 3 2-25
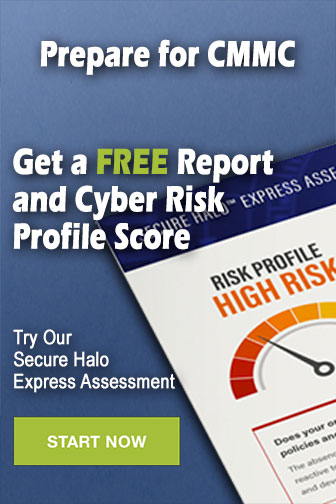