TM 9-2320-302-20
0020 00-1
UNIT PREVENTIVE MAINTENANCE CHECKS
AND SERVICES (PMCS) INTRODUCTION
0020 00
GENERAL
1.
To ensure that the M915A3 Tractor Truck is ready for operation at all times, it must be lubricated and inspected on a
regular basis so that defects may be found before they result in serious damage, equipment failure or injury to personnel.
2.
Table 1 lists the types, amounts, and temperature ranges of the lubricants required for specified intervals.
3.
Table 1 in WP 0021 00 contains systematic instructions on lubrications, inspections, adjustments, and corrections to be
performed by Unit Maintenance to keep the vehicles in good operating condition and ready for their primary mission.
4.
Table 2 in WP 0021 00 lists PMCS mandatory replacement parts, by interval.
EXPLANATION OF TABLE ENTRIES
1.
Item Number (Item No.) Column. Numbers in this column are for reference. When completing DA Form 2404
(Equipment Inspection and Maintenance Worksheet), include the item number for the check/service indicating a fault.
Item numbers also appear in the order you must perform checks and services for the interval listed.
2.
Interval Column. This column tells you when you must perform the procedure in the procedure column. Intervals are
based on calender dates.
a.
Semiannual procedures must be done once every six months.
b.
Annual procedures must be done once each year.
3.
Location, Item to Check/Service Column. This column identifies the location and the item to be checked or serviced.
NOTE
The WARNINGs and CAUTIONs appearing in your PMCS table should always be observed. WARNINGs
and CAUTIONs appear before applicable procedures. These WARNINGs and CAUTIONs must be
observed to prevent serious injury to yourself and others or to prevent your equipment from being damaged.
4.
Procedure Column. This column gives the procedure you must perform to check or service the item listed in the Item
to Check/Service column to know if the equipment is ready or available for its intended mission or for operation. You
must perform the procedure at the time stated in the interval column.
5.
Not Fully Mission Capable if: Column. Information in this column tells you what fault will keep your equipment from
being capable of performing its primary mission. If you perform check and service procedures that show faults listed in
this column, the equipment is not mission-capable. Follow standard operating procedures for maintaining the equipment
or reporting equipment failure.
GENERAL LUBRICATION PROCEDURES
NOTE
These lubrication instructions are mandatory.
1.
Recommended intervals are based on normal conditions of operation, temperature, and humidity. When operating under
extreme conditions, such as high or low temperatures, fording in water over 20 inches deep, or exposure to sand or dust,
lubricants should always be changed more frequently. Lubricants that have become contaminated will be changed
regardless of interval. When in doubt, notify your supervisor.
2.
Keep all lubricants in a closed container and store in a clean, dry place away from extreme heat. Keep container covers
clean and do not allow dust, dirt or other foreign material to mix with lubricants. Keep all lubrication equipment clean
and ready for use.
3.
Maintain a good record of all lubrication performed and report any problem noted during lubrication. Refer to DA Pam
738-750 for maintenance forms and procedures to record and report any findings.
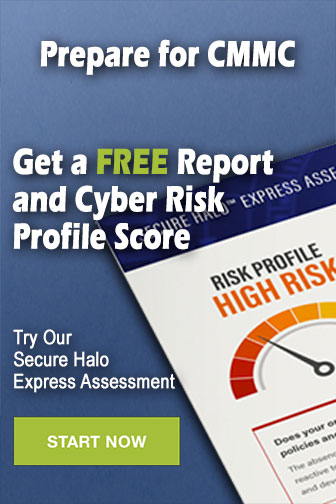